Tata Steel's green transition: Dream or dead end?
Politicians are pushing for quick subsidies to save and green the ailing Tata Steel. But is Tata still salvageable?
Published on December 9, 2024
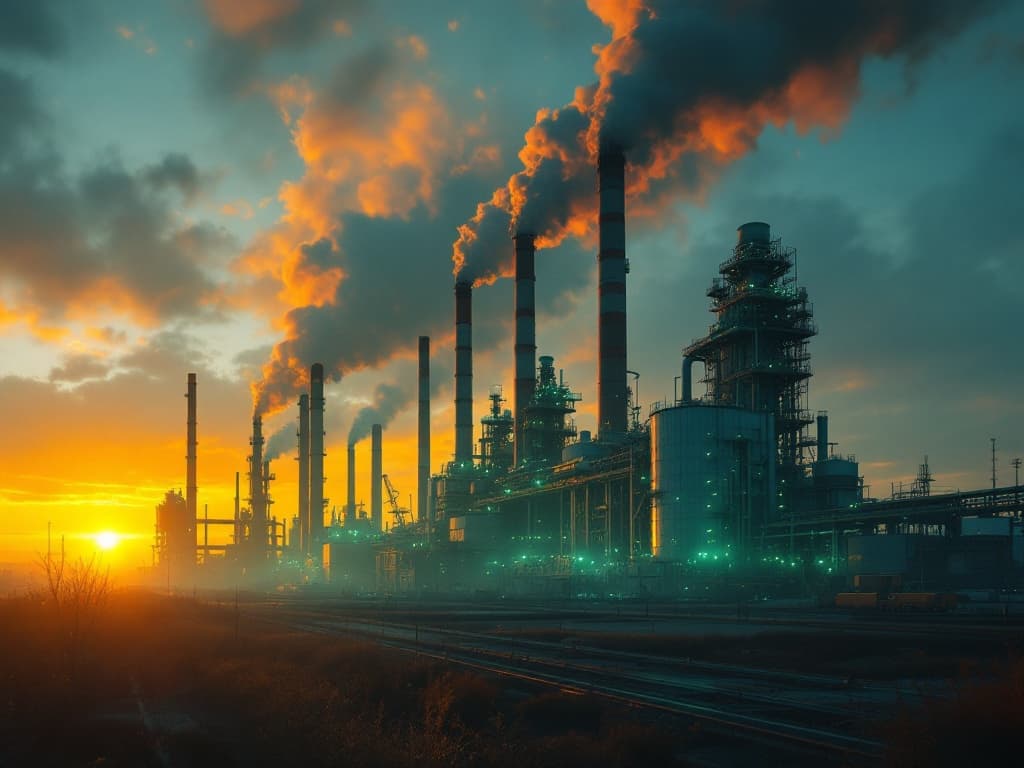
Merien co-founded E52 in 2015 and envisioned AI in journalism, leading to Laio. He writes bold columns on hydrogen and mobility—often with a sharp edge.
Tata Steel IJmuiden is on the verge of an ambitious transformation: the switch from coal to hydrogen in their blast furnace processes, a leap toward green steel. But behind this vision of the future lies a maze of problems that could quickly blur the dream. The steel market is saturated, energy in the Netherlands is more expensive than ever, and green hydrogen is virtually unattainable. The aging blast furnace process is a millstone around the company's neck, and the cost of the necessary transition is skyrocketing. As Tata Steel grapples with increasingly complex policy issues and grant applications, it keeps a slanted eye on developments in China, where new technologies are increasing productivity and reducing emissions. The question is not whether Tata Steel can get subsidies, but whether this support will be more than a stay of execution for Tata Steel.
The Chinese specter on the horizon
While Tata Steel struggles with plans for a hydrogen transition, China has made a revolutionary breakthrough in steel production. Chinese researchers led by Professor Zhang Wenhai have developed a process that reduces iron production time from 6 hours to just 3 to 6 seconds. This 'flash ironmaking' technology, which uses an advanced vortex lance system, can process 450 tons of iron ore per hour. This results in an annual production capacity of 7.11 million tons of iron - comparable to Tata Steel IJmuiden's current production. The crucial difference? The Chinese method improves energy efficiency by more than a third and eliminates the need for coal. More importantly, this technology works well with low- and medium-grade ores that are widely available in China itself. This is in stark contrast to Tata Steel's aging blast furnace process, which relies on high-grade ore that must be brought in from far away. The Chinese innovation is no laboratory dream - the vortex lance is already in commercial production, with an 80% success rate for pilot-tested technologies. This development highlights how Tata Steel is not only struggling with the transition to hydrogen but also at risk of falling behind technologically in a rapidly changing global market.
The hydrogen myth
For now, the promise of green hydrogen as the salvation for the steel industry is proving to be a mirage. By 2023, a shocking 99% of European hydrogen production was “gray” - produced from fossil fuels. Only 0.4% came from clean electrolysis. Total hydrogen production capacity in Europe was 10.8 million tons per year, of which green hydrogen electrolysis capacity was a meager 44,000 tons. For Tata Steel's ambitious plans, this is totally inadequate. The production cost of green hydrogen in the Netherlands is estimated at more than 13 euros per kilo, while competitive prices for hydrogen should be 2 euros per kilo, according to experts in the steel industry. This reality makes the hydrogen transition financially unfeasible for Tata Steel without permanent energy subsidies of at least 1.5 billion euros per year, Ines Kostić and Christine Teunissen of the PvdD argue in Parliamentary Questions. Producing green steel costs almost 800 million euros more in electricity per year in the Netherlands than in Spain, for example. These figures show that the hydrogen transition, however noble, threatens to end up in a financial quagmire from which even state aid cannot save Tata Steel.
The financial abyss
The financial situation of Tata Steel Netherlands is alarming. The company suffered a pre-tax loss of 743 million euros last year. As of March 31, 2024, Tata Steel Netherlands had only 104 million euros in bank balance, equivalent to about 1-2 months of staff costs. Since taking over the IJmuiden steel plant, the company has received no capital injection or investment from the parent company. Steel demand in Europe fell 10% last year, leading to a 20% shutdown of blast furnaces in Europe. The share of energy prices in the total cost of steel production would increase from 20% to 50% when switching to green steel. The annual electricity requirement for a production of 7 million tons of steel is about 18.3 terawatt hours - a third of the total Dutch renewable energy production in 2023. These figures paint the picture of a company that has no future in the Netherlands without massive state support. The question arises as to whether it is wise to invest billions of taxpayers' money in a company that is unwilling or unable to invest in its future.
The inevitable conclusion
While the Dutch government negotiates customized agreements and subsidies, all indicators point in the same direction: steel production in the Netherlands is becoming economically unsustainable. The combination of high energy costs, lack of green hydrogen, outdated technology and international competition makes the future of Tata Steel IJmuiden extremely uncertain. China's technological breakthrough demonstrates how the global steel industry is evolving, while Tata Steel is stuck in a costly transition process that may never become profitable. Production costs of green steel will remain structurally higher in the Netherlands than in countries with cheaper renewable energy. Shifting production to regions with better conditions for green steel production seems inevitable. The question is not if, but when this reality will be recognized. For the 9,000 workers, there is some perspective: historical data shows that 80% of industrial workers find new employment within five months. The conclusion is inevitable: the combination of economic, technological and energetic factors makes the future of large-scale steel production in IJmuiden untenable, regardless of the level of state support.