Towards the factory that can operate autonomously in a dynamic product environment
Over a hundred interested parties listened to the Technology Update for the Autonomous Factory in the Experience Center of Brainport Industries Campus.
Published on November 22, 2024
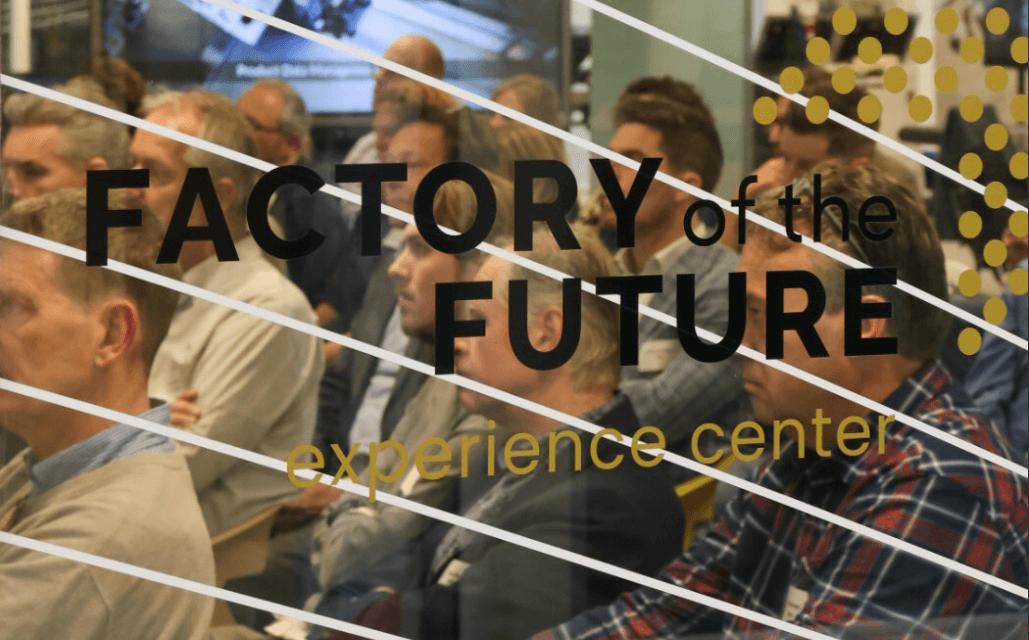
Experience Center, Brainport Industries Campus © Amber Nijdam
Bart, co-founder of Media52 and Professor of Journalism oversees IO+, events, and Laio. A journalist at heart, he keeps writing as many stories as possible.
The NXTGEN High Tech project Autonomous Factory, which runs until 2030, is about the development and implementation of process optimization in a high-tech manufacturing environment. Brainport Industries, the initiator of this national project, provided a Technology Update this Thursday at the Experience Center of Brainport Industries Campus. Led by project manager Henry Neijhorst, visitors got a glimpse of the ambitious plans of the Autonomous Factory project. Its goal? The realization of a factory that can operate autonomously in a dynamic product environment, with the help of advanced technologies.
Neijhorst said during his presentation that there are still six years to go, but that time is over before you know it. “Due to some startup setbacks here and there, we are currently a little behind schedule, but we will definitely catch up.” The program launched in 2023 focuses on developing technologies that enable the automation of manufacturing processes in a high-mix, low-volume, high-complexity environment. This focus capitalizes on the unique strength of the Brainport region: manufacturing small series with high variation.
The project consists of several building blocks, from digital simulations and twins to innovative robotics. Neijhorst: “We have a list of more than 100 issues that need addressing. Fortunately, considerable strides have been made in defining roadmaps, starting use cases, and attracting students and PhDs for research and development.”
The challenges of data and standards
One of the biggest obstacles on the road to an autonomous factory, according to Neijhorst, is the availability and usability of data. “Machines are digital, but the data they generate is often difficult to collect and standardize,” he explains. “Without a standardized approach, it is difficult to effectively deploy technologies such as simulation, predictive maintenance or OEE dashboards.”
The program is, therefore, working on a solution that applies industry standards for data exchange so that different systems and vendors can easily work together. “Only when this building block is in place can we allow the other technologies to flourish,” Neijhorst said.
The Experience Center as a testing ground
A striking aspect of the program is using the Experience Center at the Brainport Industries Campus as a test site. Here, existing demonstrators are linked to solve integration issues and test technologies in a prototype factory. Neijhorst: “An autonomous factory is more than a collection of separate cells; it is about cooperation between all systems. By integrating demonstrators, such as AGVs and operator solutions, we create an environment to address realistic problems and develop solutions.”
The program already has several use cases that contribute to the autonomous factory. One example is a TU/e master's student's research on the simulation of packaging lines. This case not only provided valuable insights but also inspired the student to start his own company in robotic solutions for the agribusiness industry.
A view of the future
The project's ambition extends beyond the Netherlands. Neijhorst: “What we develop here can have a global impact. Our high mix, low volume approach is unique and allows us to distinguish ourselves.” The end goal is an autonomous factory that not only tests technology but actually implements it in existing production facilities.
With six years to go, much work remains to be done. Still, Neijhorst looks ahead optimistically: “We know where we are working toward. The path may still change, but the end goal is clear. And that is enormously motivating for everyone who contributes to it.”