Solving dynamic challenges in next-generation cable slabs
How Demcon’s modeling framework enhances high-tech system performance
Published on February 15, 2025
Koen Franse, Demcon
Bart, co-founder of Media52 and Professor of Journalism oversees IO+, events, and Laio. A journalist at heart, he keeps writing as many stories as possible.
In high-tech systems, increasing performance demands expose components to higher forces and accelerations, creating unforeseen challenges. Among these components, cable slabs - essential for transmitting power, air, water, and cooling fluids between moving parts - experience significant dynamic effects that can impact precision, durability, and operational efficiency. Recognizing these challenges, Demcon Multiphysics has developed an advanced modeling framework that enhances the understanding and optimization of cable slab behavior.
At the forefront of this development is Koen Franse, a Multiphysics Engineer at Demcon’s Eindhoven branch, specializing in structural mechanics and dynamics analysis. In a recent talk for the DSPE community, he detailed the rigorous testing and modeling efforts aimed at mitigating dynamic issues in cable slabs. "Cable slab dynamics are quite complex, especially once you want to simulate them due to non-linearity in the system," Franse explained. With a test setup capable of reaching accelerations up to 600 m/s², Demcon has made substantial progress in optimizing cable slab design, ensuring that high-tech systems operate at peak efficiency.
The role of cable slabs in high-tech systems
Cable slabs are vital in advanced systems, facilitating the supply of essential resources while ensuring high precision and reliability. However, as these systems evolve, they are subjected to increasingly high accelerations, which can introduce undesirable dynamic effects. These effects manifest in various ways, including:
- Disturbance forces: Excessive movement can transmit unwanted forces to connected components, affecting precision.
- Wear and damage: Friction between cable slab layers can cause long-term degradation.
- Particle generation: In cleanroom environments, material wear from friction poses a contamination risk.
Understanding these effects is crucial for optimizing cable slab design, and Demcon has been at the forefront of tackling these issues through experimental testing and computational modeling. "The whole idea of the work at Demcon that we do with cable slabs is to get as much insight into their dynamical behavior as possible, which we can use to make better design decisions," Franse stated.
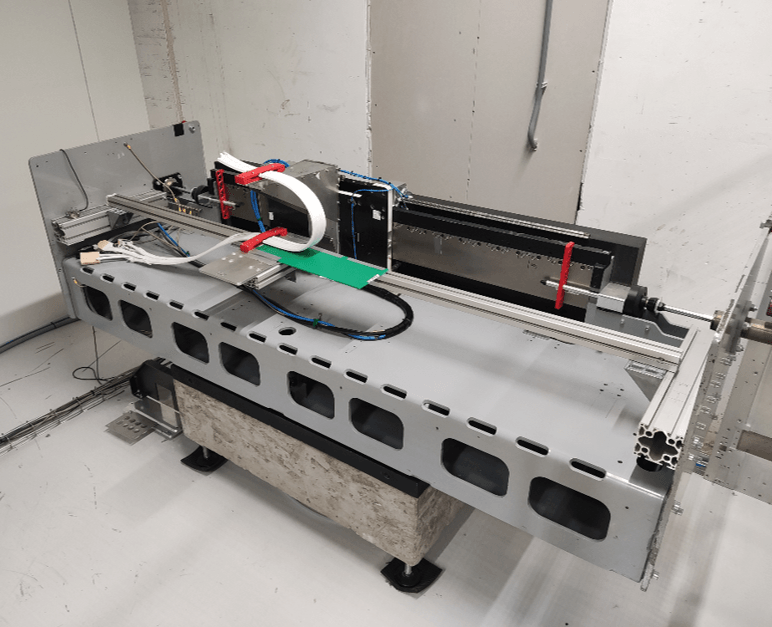
Geweldenaar © Demcon
Testing cable slabs: The ‘Geweldenaar’ setup
Demcon has relied on physical testing to analyze cable slab behavior for years. Their in-house testing facility, known as the ‘Geweldenaar,’ can simulate extreme accelerations, providing real-world data on cable slab performance. Engineers can use high-speed cameras, accelerometers, and load cells to capture intricate details of how cable slabs respond to high accelerations.
One key issue Demcon encountered was ‘slapping’ behavior, in which the cable slab that was tested for the customer started resonating at certain frequencies and colliding with the supporting walls with high-impact forces. Initially observed at 60 m/s², this effect became more pronounced as setpoint accelerations reached 100 m/s². "We saw that the cable slab started slapping against the sidewalls, generating a lot of noise and disturbing forces," Franse explained. Such behavior can cause excessive noise, increase wear, and compromise system stability.
While testing provides invaluable insights, it has limitations. Hardware constraints and long setup times make it difficult to test multiple design variations quickly. Recognizing this, Demcon sought a more efficient solution through computational modeling.
Developing a computational model: Efficiency meets accuracy
Simulation presents a powerful alternative to physical testing, allowing for rapid iteration and deeper insight into dynamic behavior. However, modeling cable slabs is challenging due to:
- Complex material properties: Cable slab components like TPU/PTFE hoses show frequency-dependent behavior and copper wire in power cables is complex to model due to its layered configuration.
- Contact interactions: Multiple components interact dynamically, adding computational complexity.
- Large deformations: Significant bending and movement requires nonlinear solvers and small time increments for correct simulation.
To overcome these challenges, Demcon worked with its customer to develop a reduced finite element model (FEM) that maintains accuracy while significantly improving computational efficiency. A conventional FEM for cable slabs could involve up to a million degrees of freedom, making simulations slow and resource-intensive. By simplifying the geometry and reducing elements, Demcon’s model cut this down to ‘just’ 300 degrees of freedom, enabling much faster analysis. "The goal was to simplify it as much as possible to reduce computation time and power while still capturing the dynamics correctly," Franse emphasized.
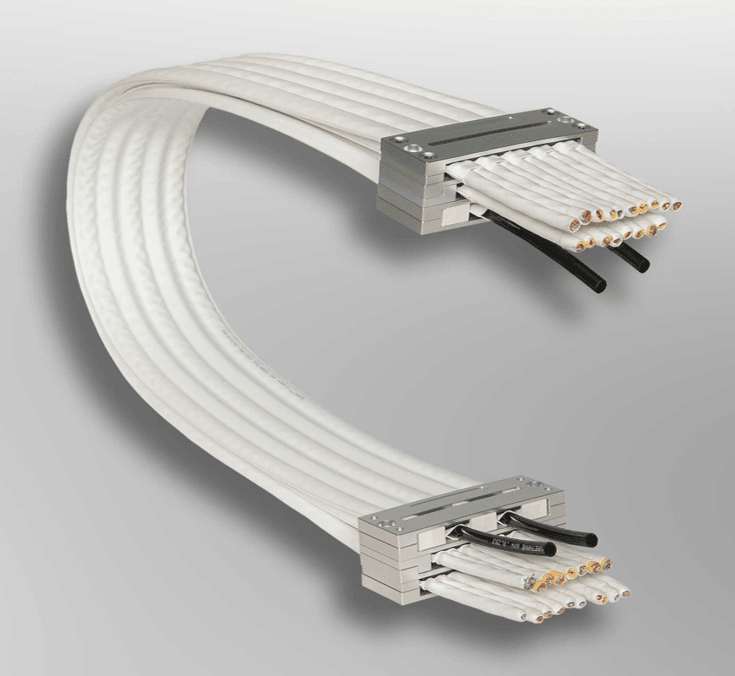
Cable slab, © Demcon
Validation: Bridging simulation and reality
To ensure their simplified model accurately reflected real-world behavior, Demcon conducted extensive validation against physical test data. Their approach included:
- Testing a single-layer slab: Using accelerometers, engineers compared measured accelerations with simulated results. The model successfully replicated observed slapping frequencies.
- Scaling up to multi-layer slabs: The model continued to perform well with additional complexity, accurately predicting dynamic responses across six-layer configurations.
- Comparing acceleration profiles: Side-by-side comparisons between test and simulation data confirmed that the model could capture key dynamic effects, proving its reliability. "We proved that you don’t need a highly complex finite element model to simulate dynamics of such a system," Franse noted.
By refining their modeling approach, Demcon demonstrated that a simplified framework could effectively predict cable slab behavior, providing a powerful tool for future design optimizations.
Applying the model: Towards better cable slab designs
With a validated model in hand, Demcon can now explore optimized cable slab designs more efficiently. By tweaking material properties, geometry, and pretensioning forces, engineers can Optimize cable slab behavior and improve system reliability without requiring extensive hardware testing.
Furthermore, this approach enables:
- Faster design iterations: Engineers can test multiple configurations digitally before committing to physical prototypes.
- Cost reduction: Less reliance on expensive test setups and hardware.
- Better system integration: Insights gained from simulations can inform broader system design choices, improving overall performance. "With this method, we can perform quick design iterations without the need for expensive and time-consuming hardware setups," Franse added.
The power of combining
Demcon’s success in modeling cable slabs underscores the power of combining experimental and computational approaches. While traditional testing remains indispensable, efficient modeling frameworks allow for rapid innovation, ensuring that high-tech systems continue to push the boundaries of performance.
As industries demand ever-greater precision and reliability, the ability to accurately predict and optimize component behavior will become increasingly vital. Demcon’s work represents a significant step forward in high-tech engineering, demonstrating that even the most complex dynamic challenges can be tackled with the right combination of testing and simulation. "If you have challenges in cable slab design, we now have quite a good basis to assist you in solving these problems," Franse concluded.