Rick Schneiders, Head of Future Foods at Siemens: ‘Collaboration and innovation are essential for the future of vertical farming’
Vertical farming can be crucial in the growing demand for sustainable food production. Siemens helps make vertical farms more scalable and energy efficient.
Published on November 8, 2024
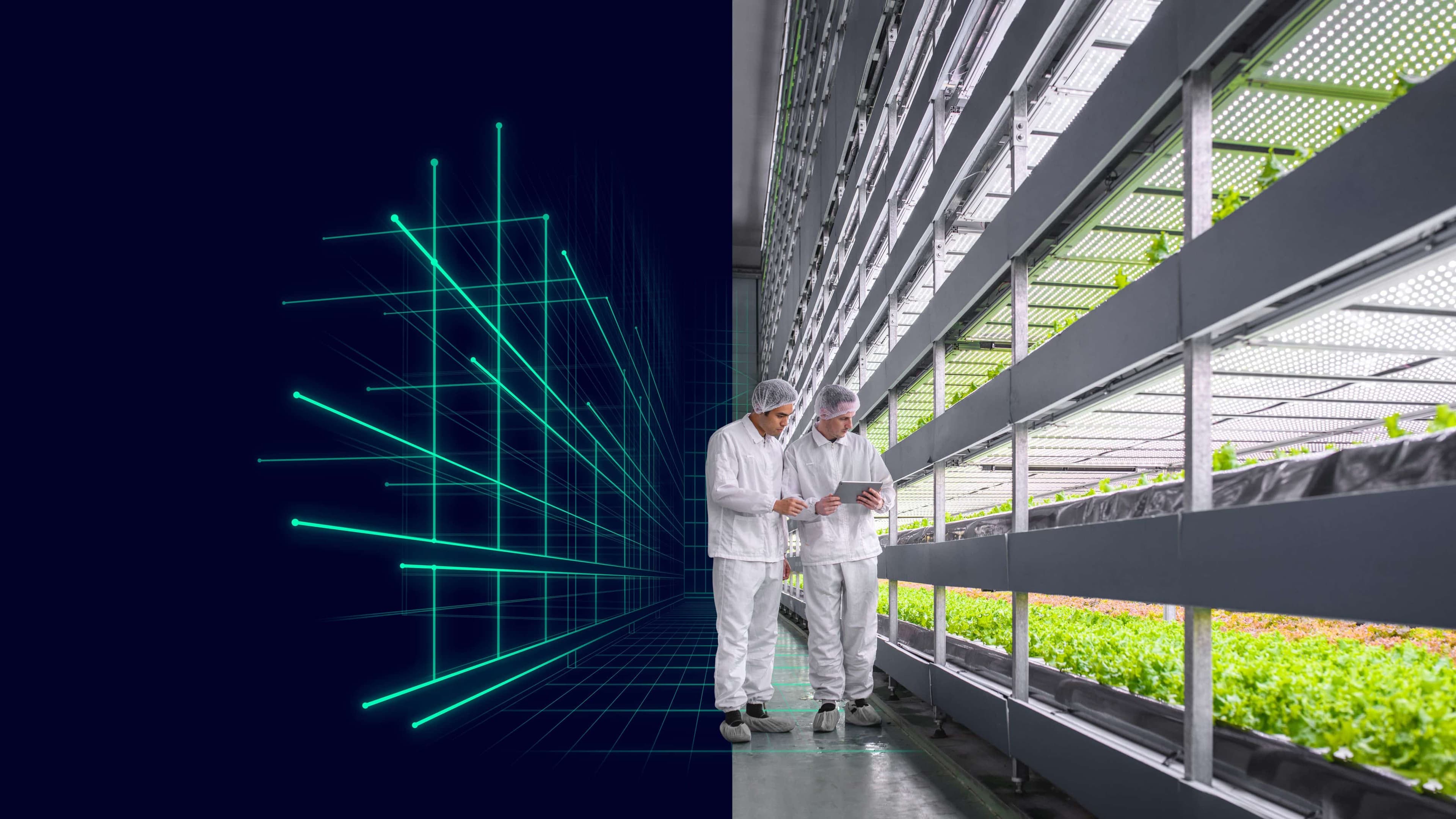
As editor-in-chief, Aafke oversees all content and events but loves writing herself. She makes complex topics accessible and tells the stories behind technology.
Vertical farming is seen as a promising alternative to the increasing demand for food. It can shorten the supply chain and sustainably produce more food with fewer resources. However, despite annual increases in investment in agricultural technology, indoor farming startups are raising less money. The focus is shifting from investing in new vertical farms to developing technologies for optimizing and maximizing the efficiency of vertical farms. This results in a general trend toward more intelligent and automated vertical farms.
Siemens is supporting the digitization of vertical farming with innovative technologies and collaborations. To strengthen these efforts, Siemens has established the Future Food team, with experts such as Rick Schneiders and Stefania Stoccuto. Stoccuto (Global Business Development Specialist for Future Food) is one of the speakers at the Vertical Farming program at the Agrifood Innovation Event on Dec. 3. We spoke to them about scalability, collaboration, and technology investment in vertical farming.
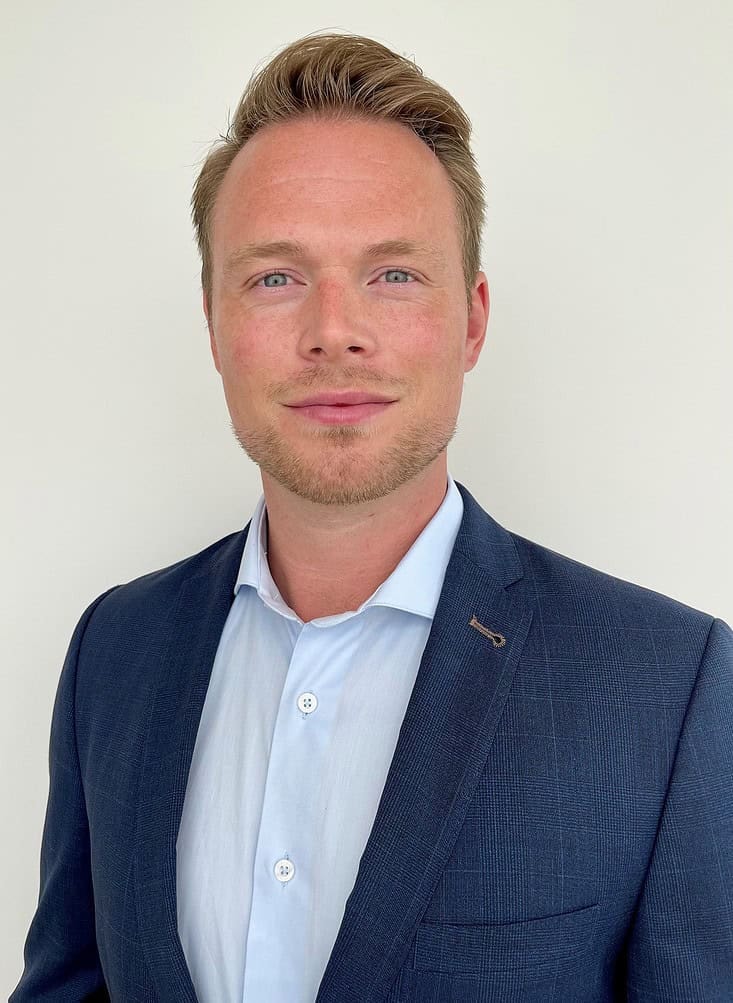
Industry-standard as a prerequisite for scalability
In recent years, it has become clear that the business model behind vertical farming is complex. Energy and labor are two factors that significantly increase costs. According to Schneiders, automation is the solution to reduce labor costs. However, automation, in turn, requires more energy. “The solution is to look from the design phase at how all the components - and therefore the different technologies - fit together.”
It is essential to determine how the different parts of a farm - seeding, harvesting, lighting, packaging - can be linked together. One of the biggest problems is that the various steps in the production process of a vertical farm currently operate independently of each other. The goal is to work toward a system where all devices and machines communicate seamlessly. Integrating all these processes within one system is challenging but necessary for scale-up. An industry standard is crucial but still largely lacking in agribusiness.
Reinventing the industry together
To overcome these challenges, the industry must reinvent itself. Schneiders said this can only be achieved when companies work together. “Together, you can achieve much more and implement smarter solutions. Look at 80 Acres in the United States. They are one of the world leaders in vertical farming. Although they are a large company, they understand the importance of a strong ecosystem.”
In this context, Infinite Acres, together with partners TTA, Signify, and SICK opened a vertical farming field lab in The Hague. This location was carefully chosen. In the past seventy years, greenhouse horticulture in the Netherlands has developed to a high level; our country is a leader in the high-quality cultivation of tomatoes, peppers, cucumbers, and soft fruits such as strawberries.
The research center combines Siemens' hardware and software with Infinite Acres' operation platform and technology. Siemens' technologies help optimize energy efficiency and automation. In the coming years, the goal is to involve more parties in the field lab to strengthen cooperation and innovation in the sector.
Schneiders: “One party specializes in lighting, another knows everything about sensors, and another builds machines that can harvest. In the lab, we think together about integrating the technology into one.” The field lab allows companies to test new technologies, and knowledge institutions are welcome to conduct research. Four mini modules are being grown; the next step is a mini farm where automation and logistics come together.
In addition, Siemens Xcelerator plays a crucial role in developing an open ecosystem driven by operational standards and open communication protocols. Stoccuto explains: “This ecosystem enables different companies, regardless of size, to access digital technologies and solutions to integrate their manufacturing processes fully. Through this collaboration, we can jointly accelerate digital transformation in indoor farming and create a powerful network of partners.”
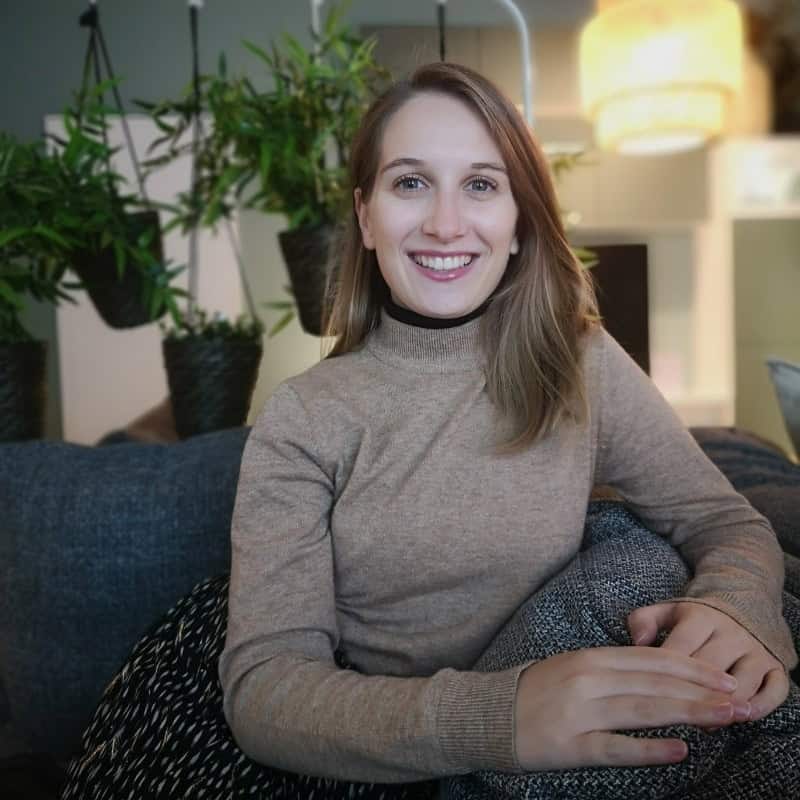
Energy optimization and automation
One of the major operational cost items in running a vertical farm lies in energy costs. To optimize this, it is essential to have full transparency of data and information by monitoring and controlling the inputs in the vertical farm that affect energy output. Stoccuto explains: “However, the creation of transparency lies not only in energy monitoring and effective energy management solutions but also in the entire sustainability and life cycle assessment strategies. Here, decarbonization and product carbon footprint transparency along the supply chain play a major role.”
Siemens' technology focuses on optimizing energy efficiency and automation in vertical farms. This is reflected in Siemens's use of hardware and software to improve energy management and automation processes. “Vertical farms, by smartly managing energy data and using renewable resources when needed, can save a lot of energy.”