Digital support transforms the manufacturing processes
“Digital work instructions improve quality, speed up learning time and increase efficiency,” said TNO's Jeroen van Oosterhout during During the Technology Update ‘The Autonomous Factory’ at Brainport Industries Campus.
Published on November 24, 2024
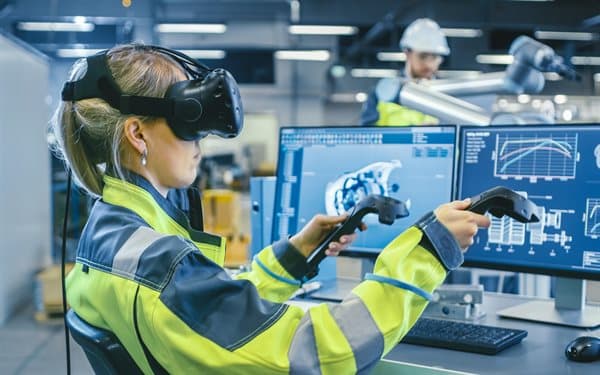
Bart, co-founder of Media52 and Professor of Journalism oversees IO+, events, and Laio. A journalist at heart, he keeps writing as many stories as possible.
The future of the factory is digital and autonomous, but the human factor remains central. That's what Jeroen van Oosterhout, Human Factors Engineer Digital Support & Cobots at TNO, argued during Brainport Industries' Technology Update. “We need to use technologies that support operators and make their work easier and more efficient,” he told a room of more than a hundred people from the high-tech manufacturing industry. The meeting took place at Brainport Industries Campus.
The challenge of variation and complexity
Van Oosterhout outlined the challenges many companies face: increasing product variation, high-quality requirements, and the need for error-free processes. “How do you ensure the right instructions reach the right employee at the right time? And how do you prevent an incorrect version of a work protocol from being used?” He believes the answer lies in smart digital support systems.
Four innovative technologies
TNO researches and develops various technologies to support operators in production processes. Van Oosterhout explained four key innovations:
- Digital instructions on a tablet or screen that guide workers step-by-step.
- Projection technology, where instructions are projected directly onto the product, reducing errors.
- Smart glasses that display information hands-free to employees.
- Augmented reality, which displays 3D instructions about the product.
A notable innovation is the use of AI tools that automatically generate construction and work processes based on 3D models. According to Van Oosterhout, this significantly lowers the entry threshold for digitization.
Results in practice
TNO has been testing these technologies extensively in working production environments in recent years. The research showed convincing benefits: operators with digital work instructions worked faster, made fewer mistakes, and needed less help. “Even MBO 2 students with digital support performed as well as MBO 4 students with paper instructions,” Van Oosterhout told us. “This opens the door to a much broader labor market.”
Another significant development is the integration of digital tools into existing production processes. “We are aiming for a universal standard for digital work instructions,” Van Oosterhout said. Although this is still in the research phase, he sees great opportunities for more straightforward implementation.
Digital revolution in full swing
Van Oosterhout concluded with a clear message: “Digital work instructions improve quality, speed up learning time and increase efficiency. This is not only an investment in technology, but also in people. It is a crucial step toward the autonomous factory.”