Building the basis for the green hydrogen economy
Thanks to a National Growth Fund grant, TU/e researchers will increase knowledge in the Netherlands about generating hydrogen.
Published on November 16, 2024
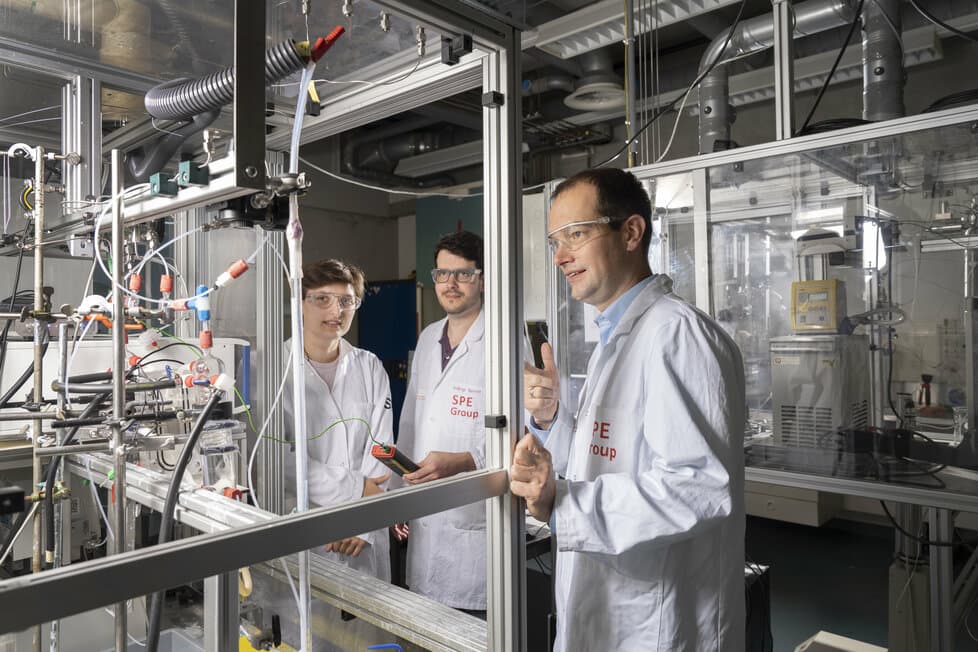
Team IO+ selects and features the most important news stories on innovation and technology, carefully curated by our editors.
Green hydrogen can be a foundation for the transition to a sustainable energy supply and chemical industry. That is the vision pursued by the National Growth Fund program Groenvermogen NL. As part of this program, the HyPRO project was recently launched, focusing on the production of green hydrogen. Being one of the 58 partners in this project, TU/e will develop new knowledge in four areas.
Source: EIRES / Sonja Knols
Hydrogen is regarded as an essential component in the energy and resources transition: Light gas can be used to temporarily store sustainably generated energy, and it can act as a building block for a chemical industry that is not based on fossil fuels.
Groenvermogen NL, an innovation program receiving €838 million from the National Growth Fund, aims to establish a national ecosystem for green hydrogen and green chemistry in the Netherlands. The overall program includes seven work packages, which, for example, deal with transport, storage, and use of hydrogen.
Making hydrogen
“But it all starts with the hydrogen production,” states Niels Deen, Professor of Multiphase and Reactive Flows at the Department of Mechanical Engineering. Deen and several other TU/e colleagues attended the so-called ‘sandbox’, a multi-day meeting where universities, knowledge institutions, government, and companies jointly shaped the HyPRO project.
From water to hydrogen
Splitting water into hydrogen and oxygen with electricity generated by solar panels and wind turbines is a logical route when thinking about hydrogen production, says Thijs de GrootThijs de Groot, associate professor of electrochemical process technology in the Department of Chemical Engineering and Chemistry, says splitting water into hydrogen and oxygen with electricity generated by solar panels and wind turbines is a logical route to hydrogen production.
“Large-scale electrolyzers for water splitting have been around for a long time. However, up until now, they have been powered by a continuous source of electricity, such as a hydroelectric plant. When we talk about green hydrogen, we have to switch to renewable electricity from sun and wind. These power sources are variable: at one instant, you might have a large supply of electricity, and later that day, perhaps you have nothing.”
“In the HyPRO project, one of the things we are looking at is how this intermittent supply of electricity influences the operation of the electrolyzer. What processes cause the degradation we witness when we frequently turn an electrolyzer on and off? And how can we improve the yield of the water splitting process?,” says De Groot.
Open call
Deen says the HyPRO project came about uniquely. “There was an open call inviting everyone who thought they could contribute anything to this topic. We sat down with 60 people for a few days to shape the outline of the program.”
It was jointly decided that the 17 research institutions and 41 companies would collaborate within five program lines. Four of these address different technologies for producing hydrogen, and the fifth line focuses on how hydrogen can fit into the future's energy system and chemical industry.
EIRES' added value
Deen says that TU/e's pooling of energy research in EIRES has certainly helped to bring TU/e to the table on the right topics.
“We already had a good idea of who was working on what within our university. For me, the fact that as a researcher, you can break free from your expertise and speak on behalf of the entire university is a clear added value of such an interdisciplinary institute.”
Within the 50 million euro HyPRO project, TU/e is researching three ways to produce hydrogen and the system integration aspect.
Who does what
Deen: “It takes a lot of green power to produce green hydrogen. That means you’re going to have a huge grid load somewhere. Colleagues at the Department of Electrical Engineering led by Koen Kok will investigate the most logical way to fit this load to the grid, for example, by combining a hydrogen production site with an offshore wind farm.”
“When it comes to the technologies used, there is a project at the Department of Applied Physics and Science Education led by Adriana Creatore on new materials for catalysts that can make the production process more efficient. At the chemistry department, Thijs de Groot will look at alkaline electrolyzers and Toni Forner-Cuenca at porous electrodes.”
“Maike Baltussen from the Department of Chemical Engineering and Chemistry and Yali Tang from my own group at Mechanical Engineering will focus on simulating electrolyzers. We can hire two PhD students and four postdocs within HyPRO,” Deen summarizes.
Optimizing electrolyzers
“One of the research topics within HyPRO coincides seamlessly with the research within my group,” says De Groot.
“We are studying alkaline electrolyzers to increase their lifetime, hydrogen yield, and flexibility. Within HyPRO, among other things, we want to work toward a good protocol to test new designs, materials, and components for electrolyzers in a standard way to enable quick statements about the expected long-term performance of a system.”
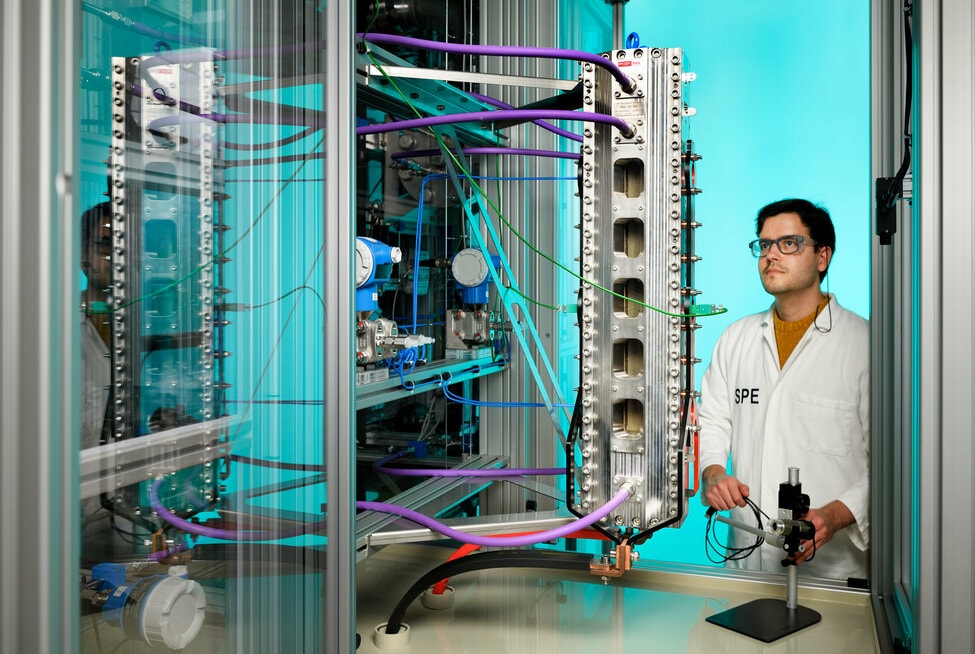
Researcher Lira Garcia Barros - Photo © Bart van Overbeeke
The perfect membrane
De Groot’s research also looks at the various components that make up the electrolyzer, intending to optimize the system. “For example, we are looking at the membranes that separate the produced hydrogen and oxygen. If such a membrane is too thick, the electrical resistance in the electrolyzer increases.”
“As a result, less hydrogen is produced. On the other hand, if it is too thin, it allows hydrogen gas to pass through, which can lead to the formation of an explosive mixture.”
“The challenge of electrolyzers is that everything is related to everything else; finding the ultimate optimum is difficult. So, the first step is to find out which knobs we need to turn in which ways to make the process suitable for large-scale and economically viable production of green hydrogen.”
Deen says that is also the goal of the HyPRO research that will be conducted in his group. “In an electrolyzer, hydrogen is created in the form of bubbles. But those bubbles introduce an additional electrical resistance. With simulations, we will map how the electrolyzer's design and use affects this resistance, with the ultimate goal of increasing the efficiency of the process.”
Most promising technology
Though there are several ways to make hydrogen, De Groot thinks alkaline electrolysis has the best papers.
“Other technologies rely on rare materials or are significantly more expensive. Therefore, it is quite likely that bulk production will be via alkaline water electrolyzers. I believe in that technology; otherwise, I wouldn’t be working on it. But there is still a lot that can be improved. Green hydrogen is still grossly expensive, which does not help its large-scale implementation.”
De Groot quickly calculates that large-scale implementation is necessary. “It starts, of course, with the question, ‘How big is green hydrogen going to be?’ We're not going to put that in cars, but mainly use it for the industry for everything that can’t be electrified, to make chemicals and green steel, for example.”
“Then you need a lot of hydrogen: we now foresee that we will need terawatts of electrolyzers by 2050. We are now at 1 to 2 gigawatts of capacity. That means we need to scale up by a factor of a thousand.”
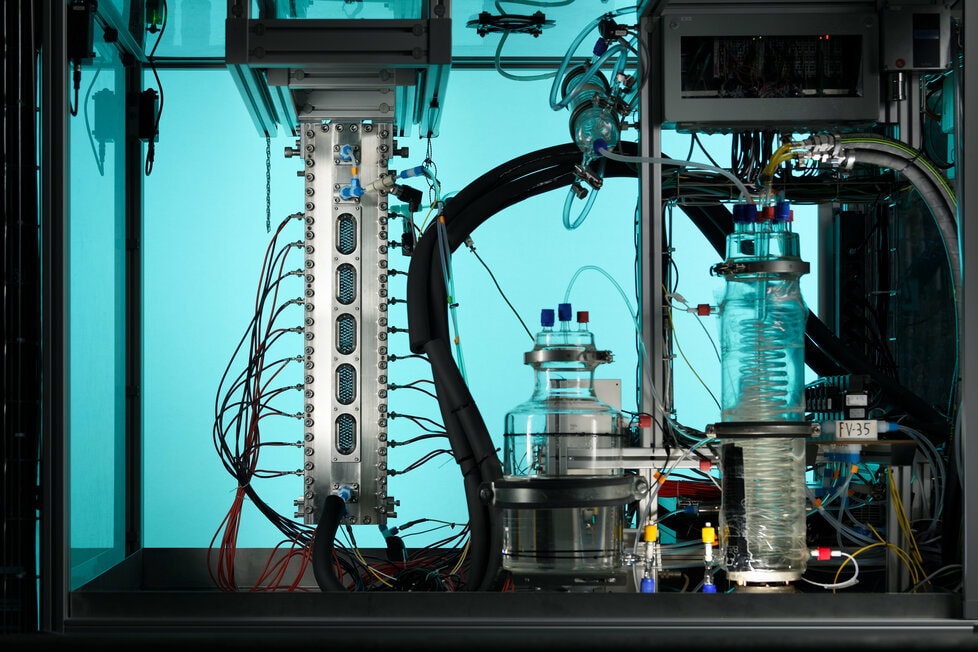
Hydrogen lab, TU Eindhoven, © Bart van Overbeeke
Fast network-building
Both Deen and De Groot believe that bringing academia and industry together is essential to accelerating this development. An initiative like Groenvermogen NL is indispensable for this.
Deen: “The good thing about the sandbox process was that it forced the scientific and business communities to listen to each other and discover together what questions exist and what tools are available to answer them.”
“Because we came together physically with 58 parties, we built a network quickly. The fact that we can now put a face with a company makes it much easier to contact each other for other questions.”
“Though I have worked in the industry and already know many parties, there are also partners involved within HyPRO I hadn’t collaborated with before, such as Battolyser Systems and AVOXT,” De Groot adds.
“The consortium is vast: it includes suppliers of complete electrolyzers and parties supplying membranes and building stacks. You need that to develop a technology that can enter the market quickly and make a real difference.”
Hydrogen as a regional competence
As part of Groenvermogen NL, De Groot announces that there will also be a program that invests in human capital in the scope of the hydrogen economy.
“Three million euros will go to the Brainport region within this framework. Nine regional companies are already involved in HyPRO, particularly in the manufacturing industry. Eventually, we hope to launch a hydrogen competence center with the Human Capital program in Eindhoven. It would only be logical to involve the regional companies we already collaborate with within HyPRO.”