Boston Dynamics' next leap: Humanoids built for the real world
With AI, locomotion, and robotic manipulation converging, Boston Dynamics is shaping a future where humanoid robots tackle real-world tasks
Published on April 9, 2025
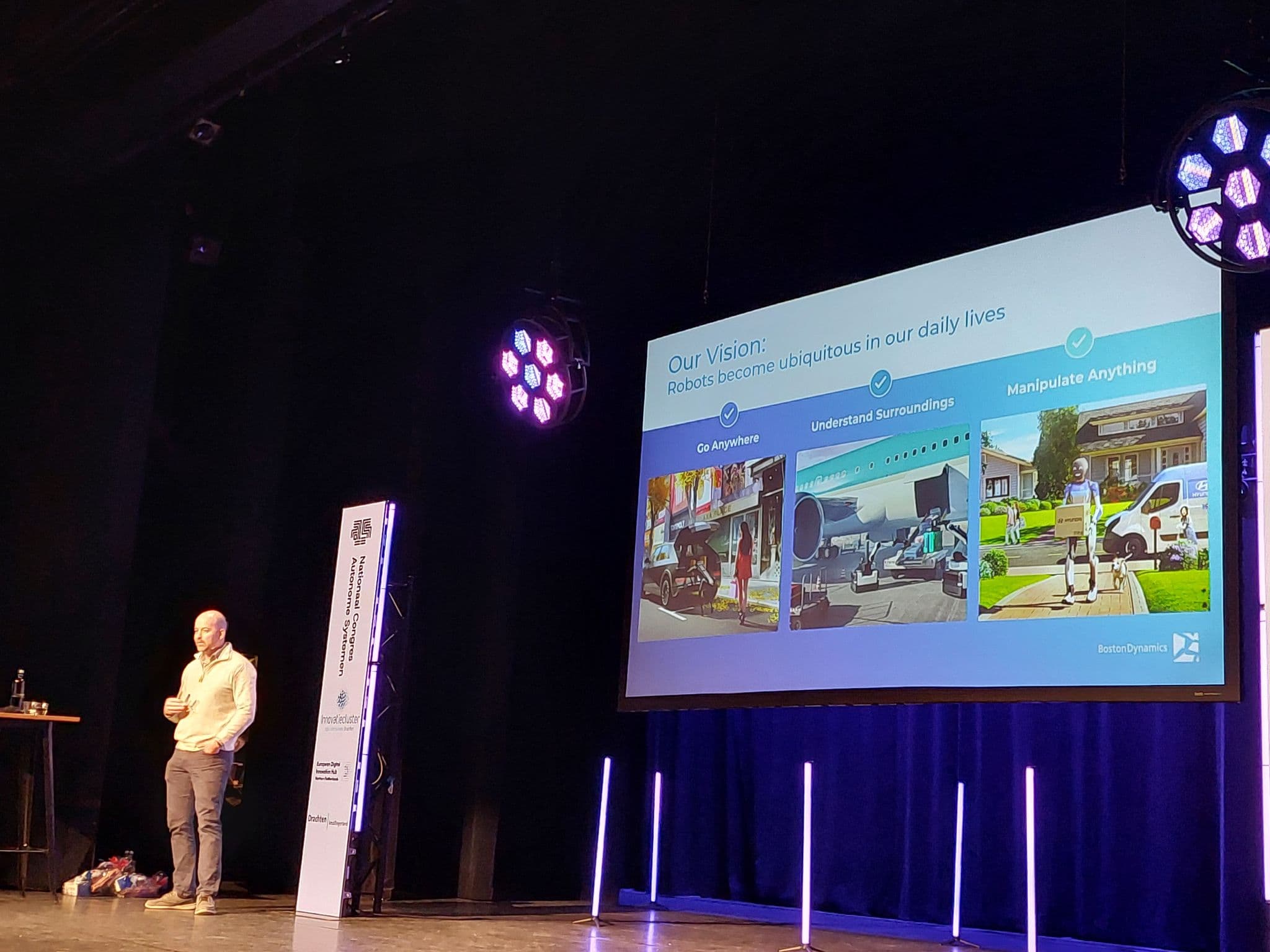
Aaron Saunders (Boston Dynamics) pitching
Bart, co-founder of Media52 and Professor of Journalism oversees IO+, events, and Laio. A journalist at heart, he keeps writing as many stories as possible.
Boston Dynamics isn’t building humanoid robots because they’re flashy; they’re building them because they’re necessary. “We humans have designed our world around us,” Aaron Saunders said. “And until we redesign the world, the fastest way to bring robots into it… is to make them more like us.”
Aaron Saunders, CTO at Boston Dynamics, isn’t shy about the ambition behind the company’s latest innovations. “AI by itself on a cell phone is only so useful,” he said in his keynote for the Dutch National Congress on Autonomous Systems. “But if you put AI inside a robot, now you can interact with the physical world.” That’s where things get truly interesting.
Boston Dynamics has long been known for its dynamic robots: Spot, the dog-like robot, and Atlas, the humanoid that flips, dances, and runs. But today, the company is entering a new phase: moving from research icons to real-world applications. And the humanoid robot is at the center of that mission.
From dancing to doing: Why humanoids?
The shift isn’t just technological; it’s philosophical. “We’re seeing a deficit in the available workforce, rising costs, and a change in what people want from work,” Saunders explained. “The jobs still need doing, but people don’t want to do them.”
Enter the humanoid robot. Unlike a custom-built automation arm or an AMR with fixed functionality, a humanoid can- at least in theory - walk into a factory built for humans and immediately begin contributing. “We think humanoid robots will find their first real product-market fit because they ‘fit like a glove’ in the world we’ve already built,” said Saunders. “A humanoid can move through a 1.5-meter corridor, pick up parts from a bin, and load a cart, no redesign needed.”
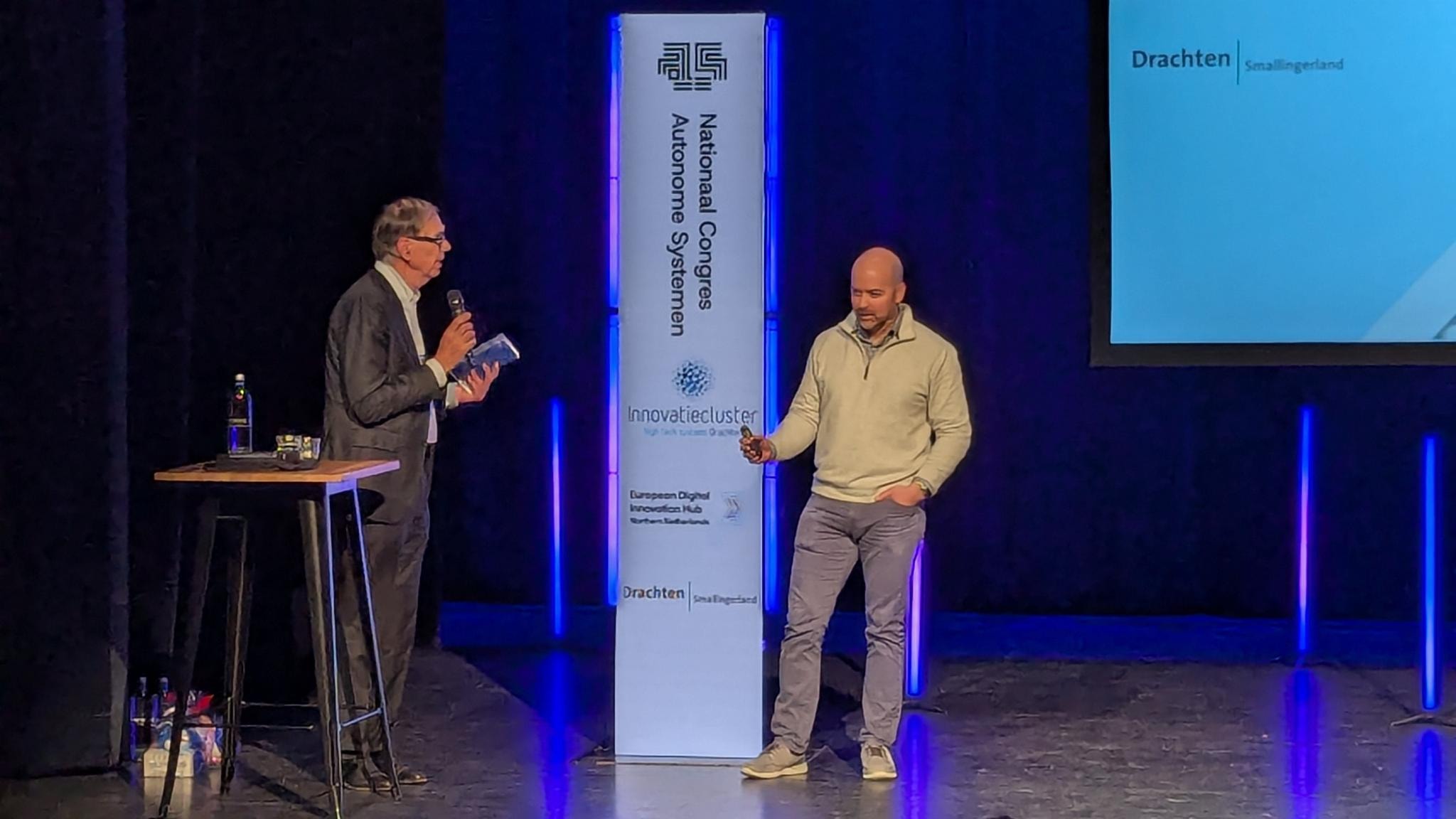
Atlas gets a day job
Boston Dynamics’ iconic Atlas robot is evolving from a platform for viral videos into a tool for productivity. The newest generation is being developed with specific industrial use cases in mind, starting with jobs in Hyundai’s factories. Think: lifting heavy, irregular parts like shock absorbers and placing them into lineside carts.
It sounds simple. It isn’t.
“These aren’t just pick-and-place operations,” Saunders emphasized. “You need precise perception, fingertip control, and adaptive manipulation. A part might be stuck, oddly shaped, or fragile. You can’t just smash and grab.” Boston Dynamics is now leveraging reinforcement learning to teach Atlas to manipulate real-world objects: training controllers entirely in simulation, based on motion-capture data.
In a recent demonstration, Atlas could extract a lightweight plastic part from a fabric pouch and place it precisely in a cart. “This would be trivial for a human, but it’s tough for a robot,” Saunders said. “That’s the level of dexterity we’re after.”
External Content
This content is from youtube. To protect your privacy, it'ts not loaded until you accept.
AI Is the game-changer
Much of Boston Dynamics’ evolution is driven by advancements in AI. Saunders described a future built around “large behavior models”: robot foundation models trained on multimodal data (images, language, motion, and more) that can generalize across tasks.
“We're going from lines of code to data pipelines,” he said. “Instead of programming a robot by hand, we feed it data - whether from simulations, teleoperation, or even YouTube videos - and let it learn.”
This leap in intelligence allows robots to move beyond repetitive, pre-scripted tasks. Boston Dynamics is already deploying Spot, its four-legged inspection robot, with AI that can identify puddles, listen for compressed air leaks, and digitize analog factory environments.
The next generation of humanoids will do the same; but with hands.
Reinvention through simulation
To build generalist robots at scale, Boston Dynamics is focusing on simulation-first development. “Every behavior we showed, from grasping a part to spinning on the ground, was generated in simulation using reinforcement learning,” Saunders explained. “We don’t need to code it. We don’t even need to demonstrate it in the real world.”
This approach speeds up development and creates more robust robots. The simulation can randomize factors like friction, object placement, and lighting, so when the robot encounters the real world, it has already passed all training sessions and is ready to go.
One recent milestone: a robot arm that successfully picks up dozens of different objects - light, irregular, or slippery - using a policy trained entirely in simulation. “You’re seeing emergent behavior, subtle fingertip grasps, and retry strategies,” Saunders said. “It’s no longer smash-and-lift. This is the future of manipulation.”
The road ahead: From 100 to millions
While humanoids are still in early deployment, Boston Dynamics is clear-eyed about the timeline. “The Rosie the Robot dream is still a ways off,” Saunders said, referencing the Jetsons-style domestic helper. “But robots doing real work in factories? That starts next year.”
Getting from prototype to mass adoption requires more than cool tech. It requires a feedback loop. Every deployed robot teaches the company something new about perception, manipulation, or deployment, and that data goes back into the next version.
“This virtuous cycle of deployment, learning, and iteration is how we get there,” said Saunders. “Robots aren’t going to take all our jobs. They’re going to fill in the gaps, and free us up to do more valuable things.”